Functionality, surface, strength
The abbreviation RIM stands for Reaction Injection Moulding: it thus actually applies for any liquidly injected PU material, but as a generic term, RIM is mainly established for thin-walled, impact resistant, energy-elastic components.
Out of a slightly foaming mixture of raw materials you can produce almost compact micro cellular components, often reinforced with fibres / fillers. Various adjustments of hardness are possible: The classical hardness ranges from 50 to 70 Shore D for stable components with good strength, high surface qualities and low abrasion.
Conventional purorim® systems are set to short cycle times and therefore have a short potlife of a few seconds. According to your machinery we can adjust the formulations to longer, less reactive settings.
Above that, purorim® systems are also used in the composites technology. Here, too, the focus lies on the high surface qualities: Fibre reinforced components can be made paintable in only one step by overflowing them with a thin purorim® layer.
- Bumpers
- Fenders
- Automotive roof modules
- Housing parts
- Belt covers
- Glass encapsulations
- Covering parts
- Saddle trees
- …
- Thin-walled and large components possible
- Hardness Shore A 40 to D 80
- Rigidity 5 to 50 N/mm²
- Adjustable reaction profile
- Applications with fillers, i. e. short glass fibre, wollastonite or barium sulfate
- Self-releasing setting possible
- Systems for overmoulding using RIM technique to create paintable surfaces (i.e. on composite substrates)
- Rail vehicle construction: DIN 5510
- Automotive industry: FMVSS 302
- Floor covering: DIN 4102 B-1
- UL-94-V0, DIN 4102 B-2, EN 13501 E
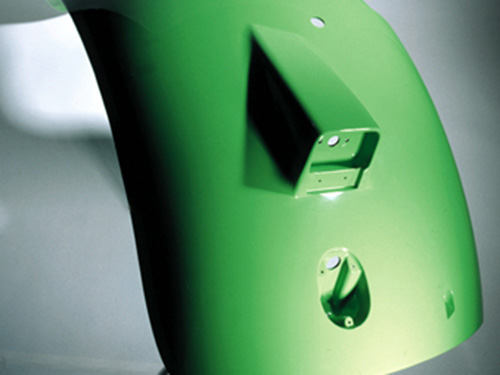

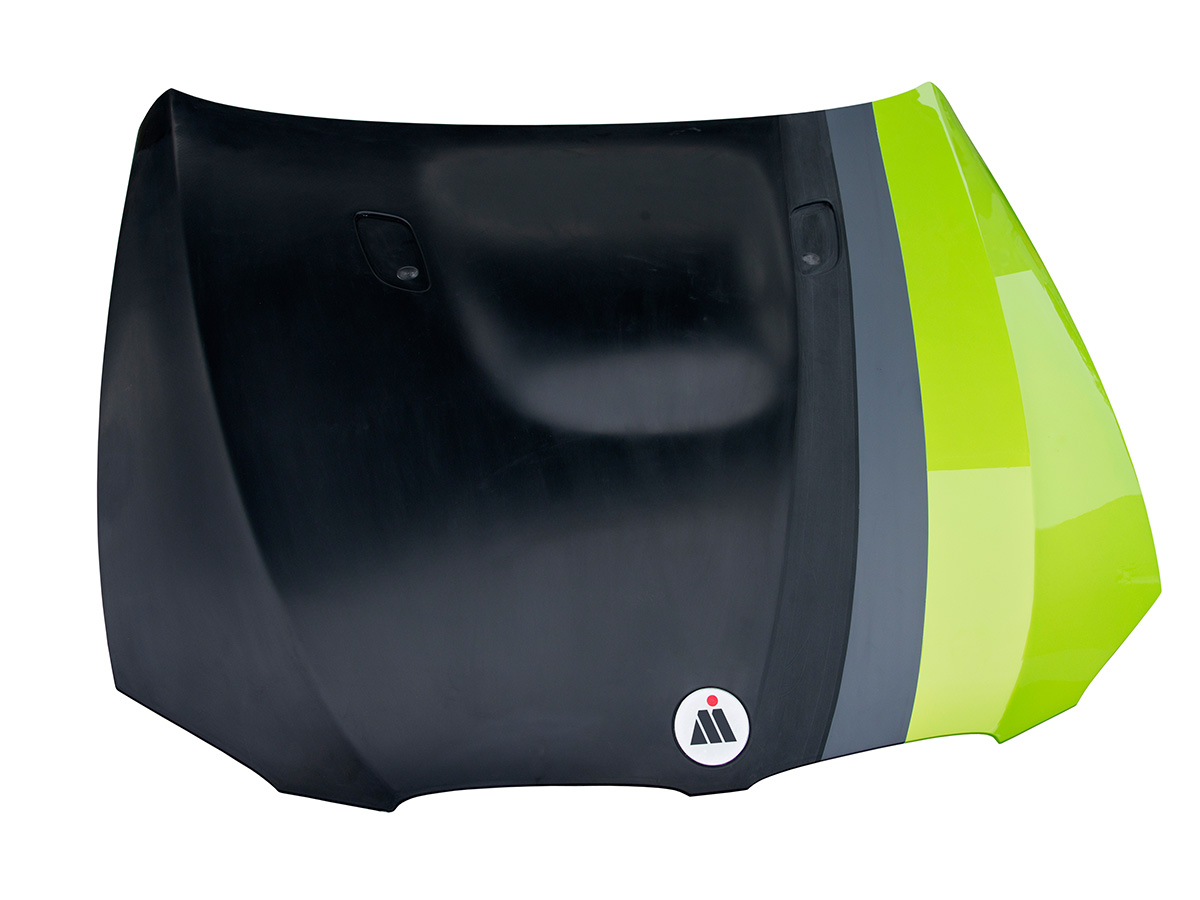
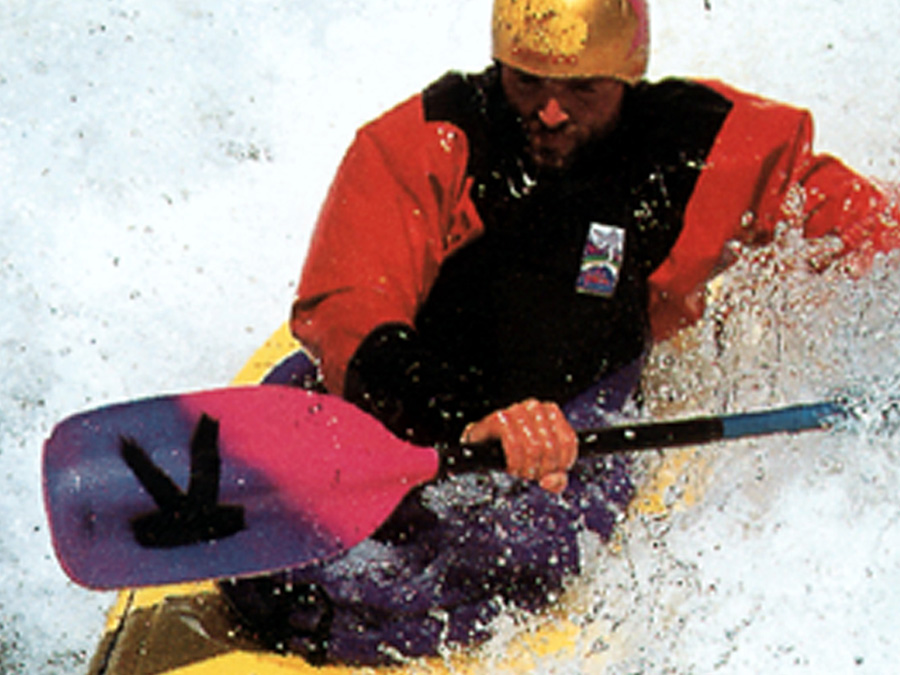
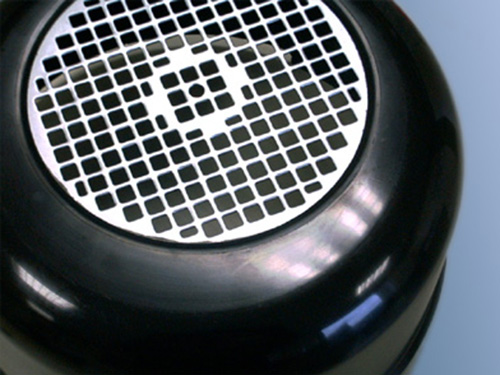
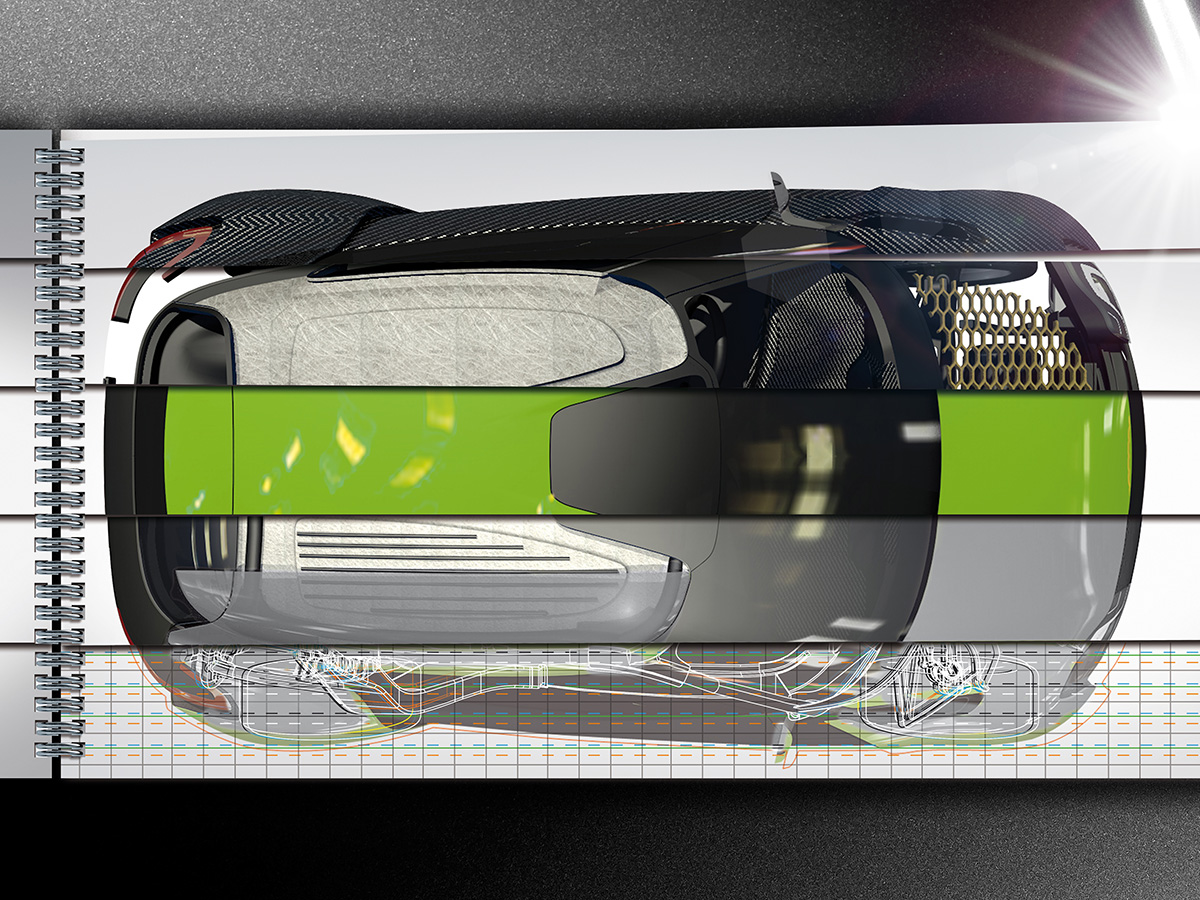