Funktionalität, Oberfläche und Festigkeit
Die Abkürzung RIM steht für Reaction-Injection-Moulding: Sie gilt somit eigentlich für alle flüssig injizierten PU-Werkstoffe, hat sich aber als Oberbegriff vor allem für dünnwandige, schlagzähe, hartelastische Formteile durchgesetzt.
Aus einem leicht geschäumten Rohstoffgemisch werden annährend kompakte, mikrozellulare Bauteile hergestellt, oft verstärkt mit Füllstoffen. Hierbei sind verschiedene Härteeinstellungen möglich: Der klassische Härtebereich liegt bei 50 bis 70 Shore D für stabile Bauteile mit guten Festigkeitseigenschaften und hoher Oberflächenqualität mit geringem Abrieb.
Herkömmliche purorim®-Systeme sind auf kurze Zykluszeiten eingestellt und verfügen somit über kurze Topfzeiten von wenigen Sekunden. Je nach Ihrem Maschinenpark können wir unsere Formulierungen aber auch auf längere, weniger reaktive Einstellungen anpassen.
Darüber hinaus werden purorim®-Systeme auch in der Composite-Technologie eingesetzt. Auch hier steht die hohe Oberflächenqualität im Mittelpunkt: Die faserverstärkten Bauteile können durch Überfluten mit einer dünnen purorim® Schicht in nur einem Arbeitsgang lackierfähig gemacht werden.
- Stoßfänger
- Kotflügel
- KFZ-Dachmodule
- Gehäuseteile
- Riemenabdeckungen
- Scheibenumguss
- Abdeckungen
- Sattelbäume
- …
- Dünnwandige und großflächige Bauteile möglich
- Härte Shore A 40 bis Shore D 80
- Festigkeiten 5 bis 50 N/mm²
- einstellbares Reaktionsprofil
- Füllstoffanwendungen mit z. B. Kurzglasfasern, Wollastonit oder Schwerspat
- selbsttrennend möglich
- Systeme zum Übergießen im RIM-Verfahren zur Erzeugung lackierfähiger Oberflächen (z.B. auf Composite Substraten)
- Schienenfahrzeugbau: DIN 5510
- Automobilindustrie: FMVSS 302
- Bodenbeläge: DIN 4102 B-1
- UL-94-V0, DIN 4102 B-2, EN 13501 E
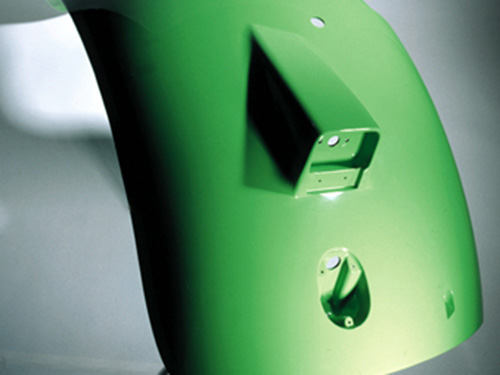

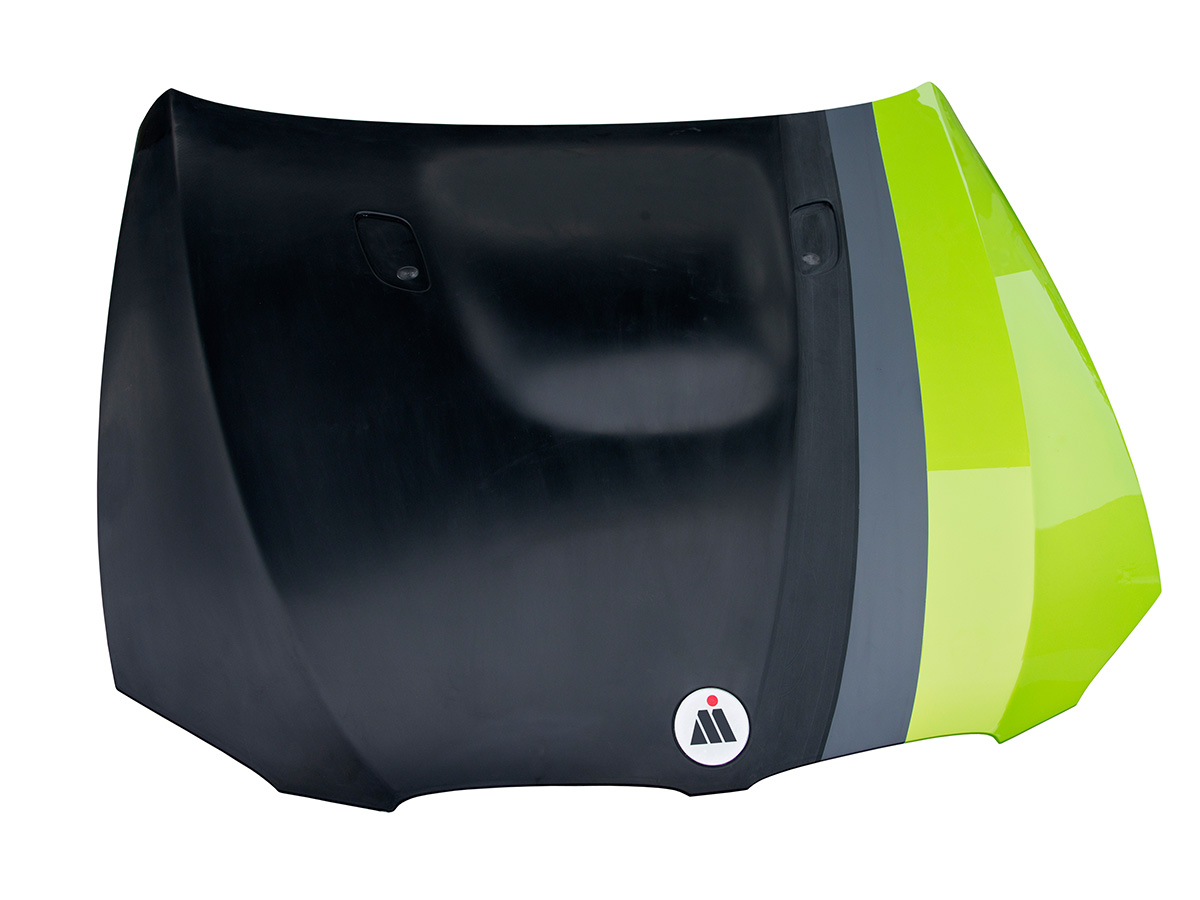
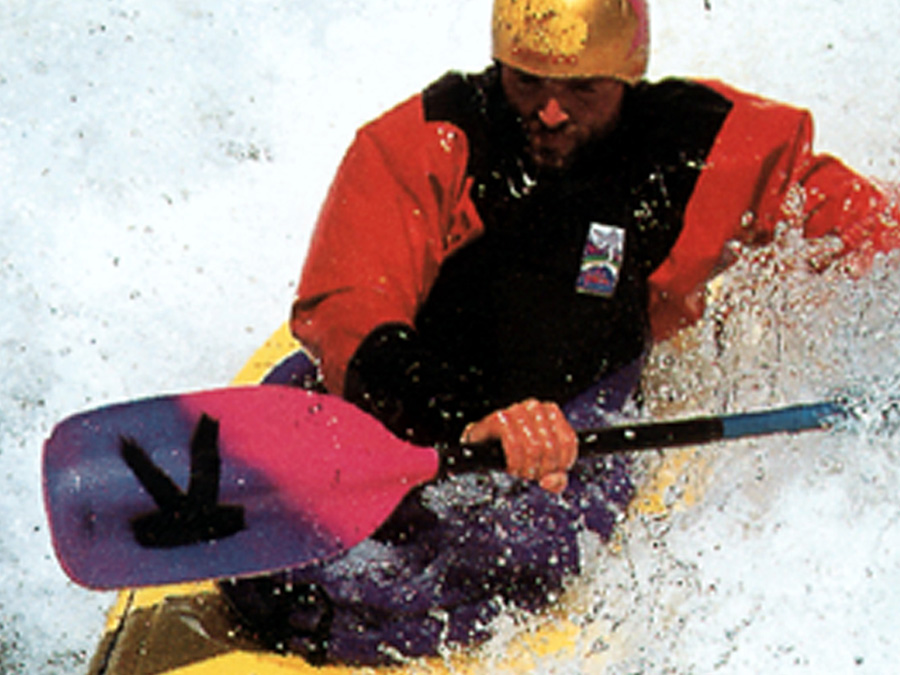
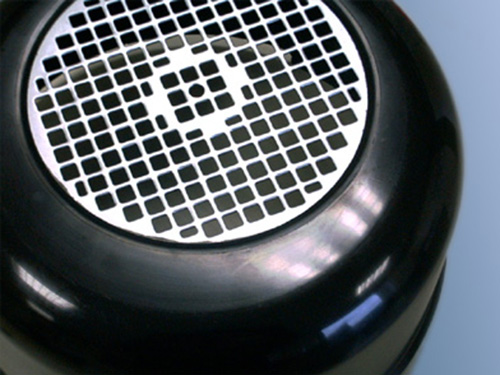
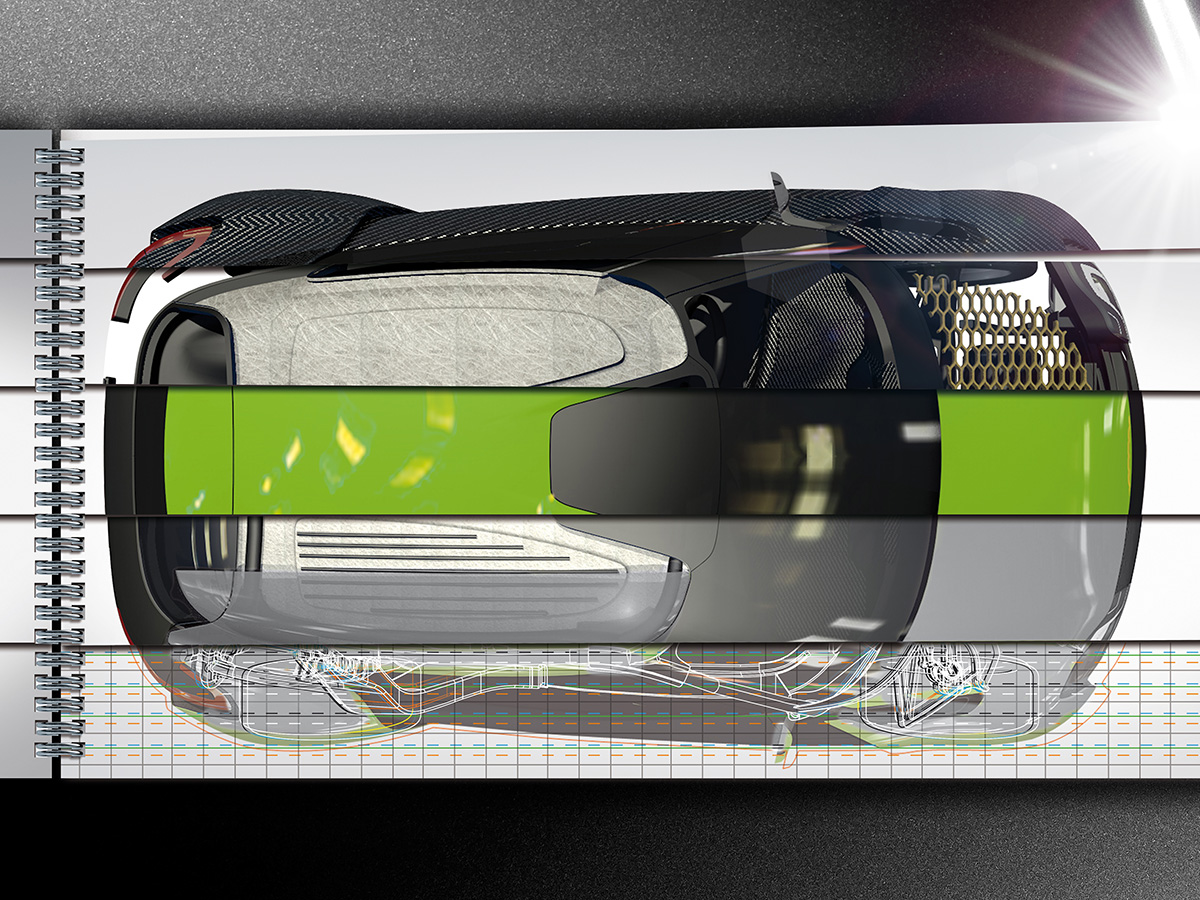