Lightweight construction with PU composites
In times of climate protection, energy saving and resource conservation, the subject lightweight construction has become a mega-trend during the last years. We meet these challenges with smart material combinations i.e. sandwich composites of puropreg® matrix systems and glass fibres combined with paper honeycomb cores. In spray technique, components with high bending stiffness and low weight can be realized. LFI processing is an additional production version, with or without core material. High-end lightweight solutions can be achieved by compact puropreg® matrix systems and their processing via spraying, wet pressing or RTM technique. Also a combination with carbon fibres is possible.
You can also get our composites components with sophisticated surface refinement: supported by multimaterial/hybrid solutions with appropriate PU casting systems i.e. puroclear® or purorim® in combination with high-quality moulds.
PU composites with puropreg® can be applied in various fields – next to the automotive sector also in the areas of commercial vehicles, construction and agricultural machines and, with appropriate flame protection, in railway vehicle manufacturing.
- Honeycomb sandwich components for light-weight and at the same time stiff rear shelves, sunroofs and load floors
- Sandwich components with waterproof honeycombs for exterior applications (i.e. bonnets)
- Monolithic fibre composite components combined with thermoplastic foils for body parts
- High-performance fibre composites with glass fibre, natural fibre but also carbon fibre reinforcements (in RTM technology)
- ...
- Moulded part density of 450–1100 kg/m³
- Fibre content from 30 % by weight to > 50 % by volume
- Blowing agents: usually water
- Reinforcing materials
- Glass fibre rovings
- Glass fibre mats, woven and non-woven fabrics
- Carbon fibres
- Natural fibres (hemp, sisal, etc.)
- Honeycomb materials for sandwich structure components
- Paper honeycombs
- Waterproof paper honeycombs
- Flame protected honeycombs
- Plastic honeycombs
- Aluminium honeycombs
- Foam cores (i.e. purotherm® rigid foam)
- Systems with a wide processing window for big components
- Usage of polyols based on renewable resources
- Self-releasing with good lamination properties at the same time
- UV stability for dark colours
- Automotive: FMVSS 302
- Aircraft construction: FAR 25853, ABD 0031
- Construction industry: DIN 4102 B2, E 13501 E
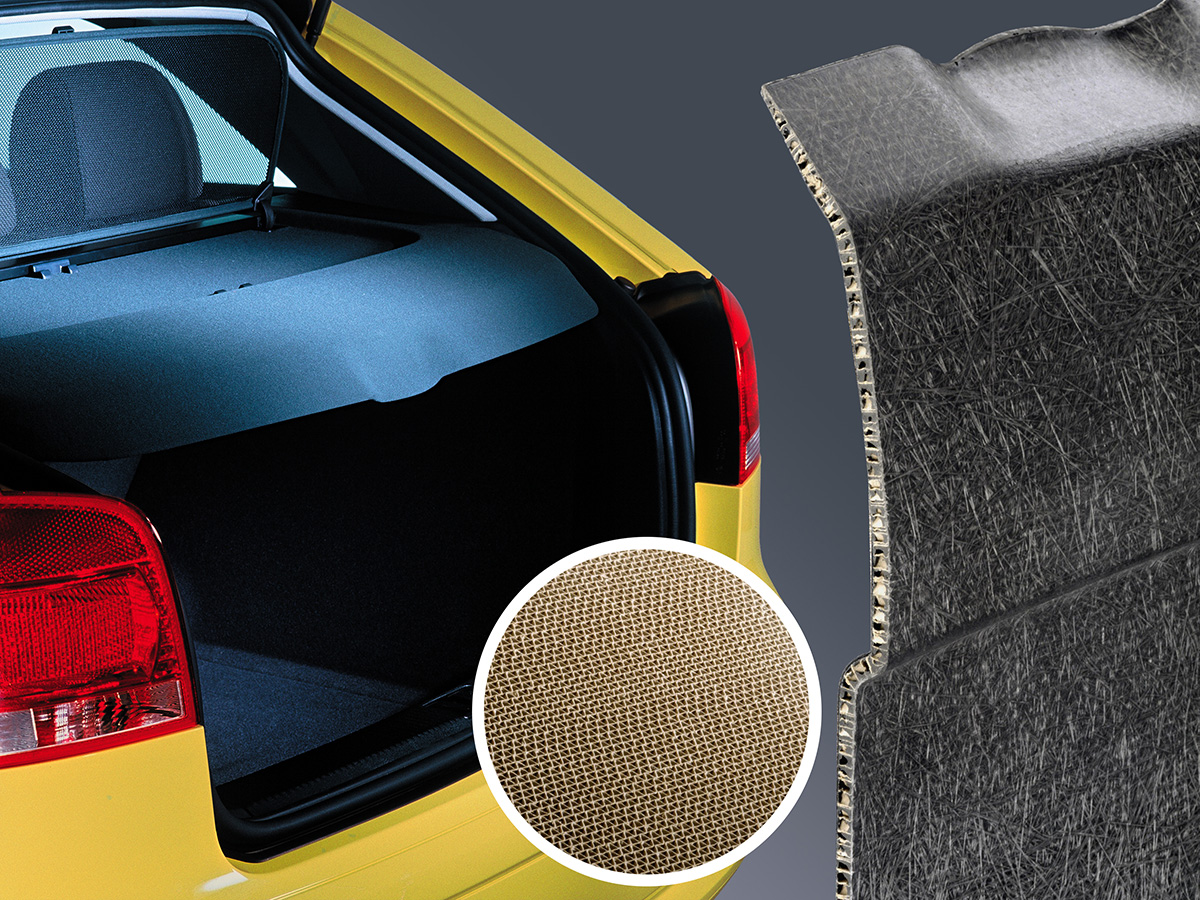
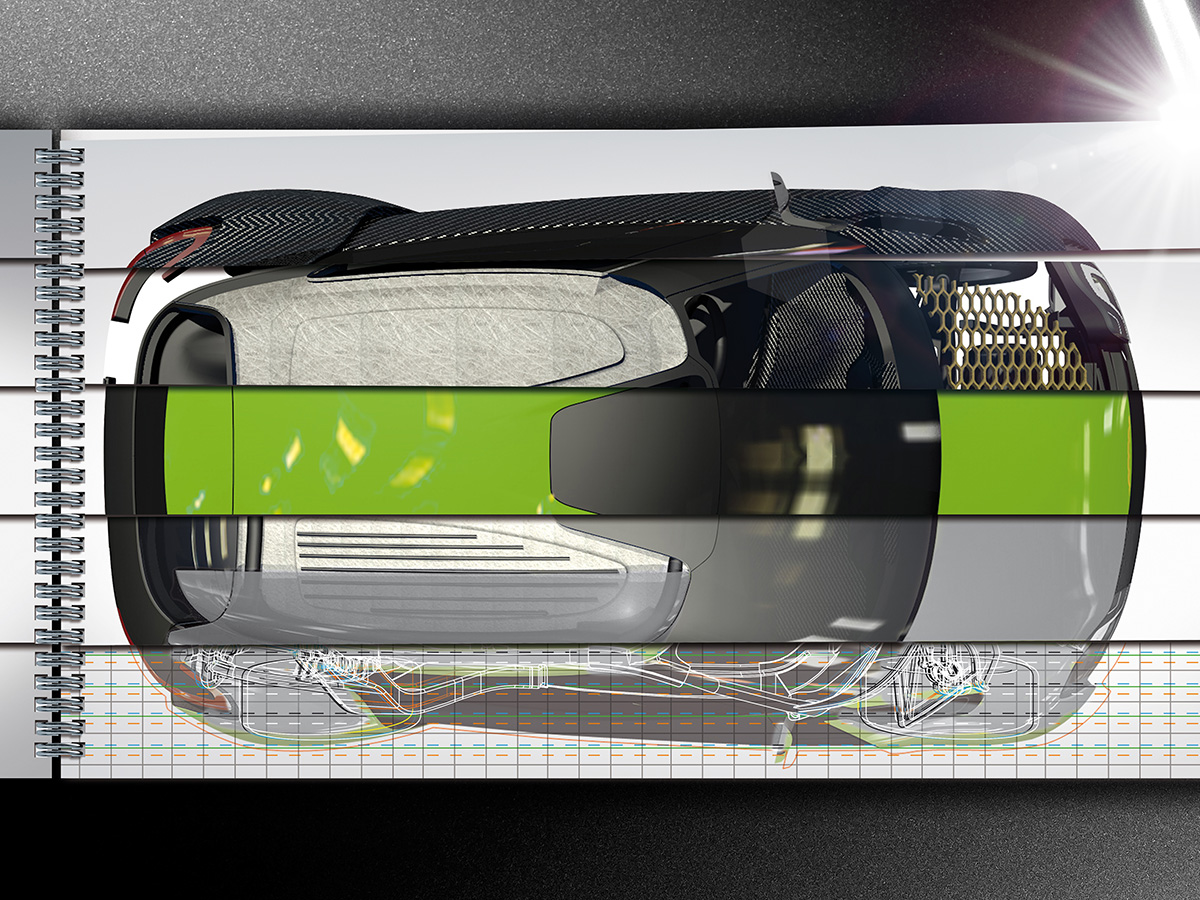
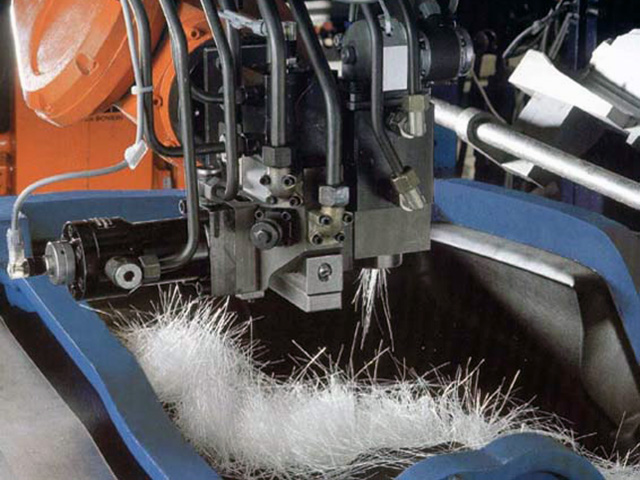
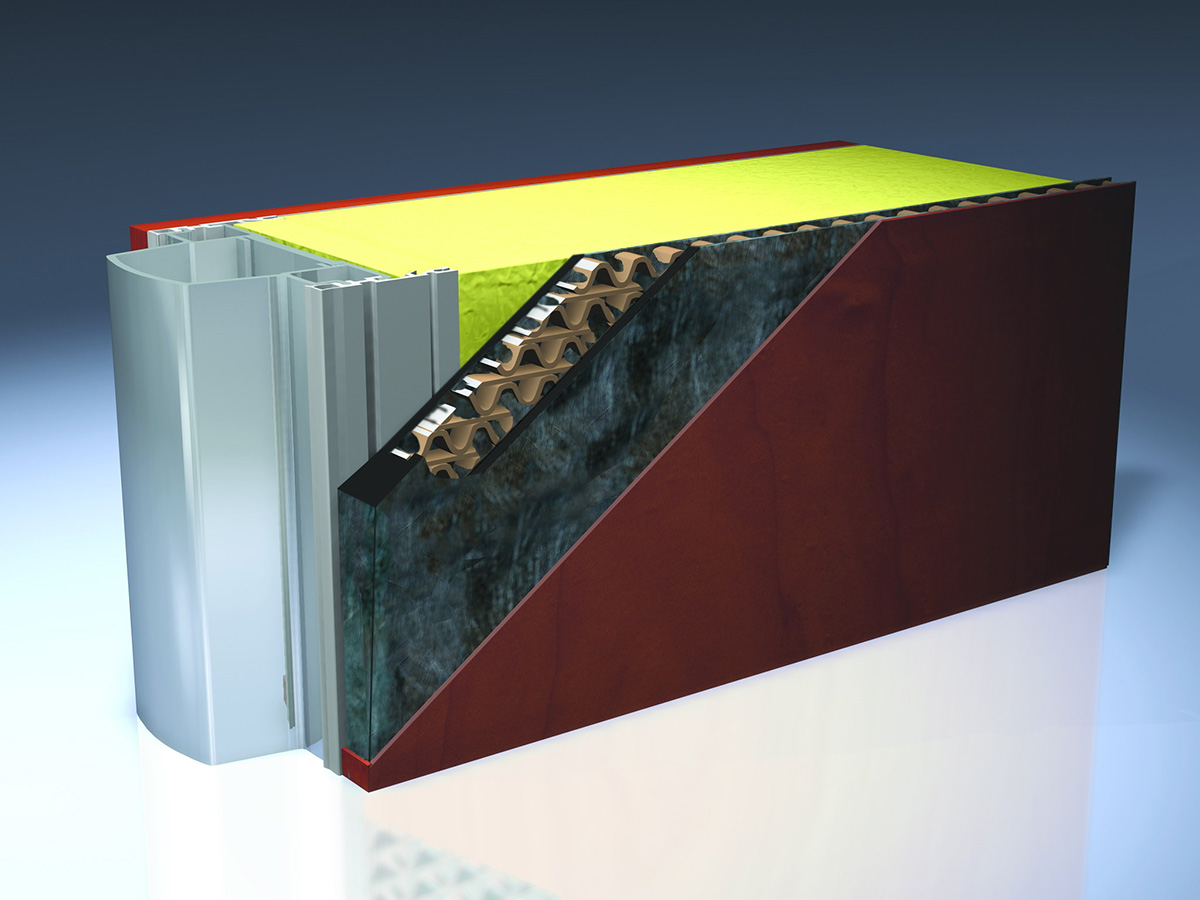
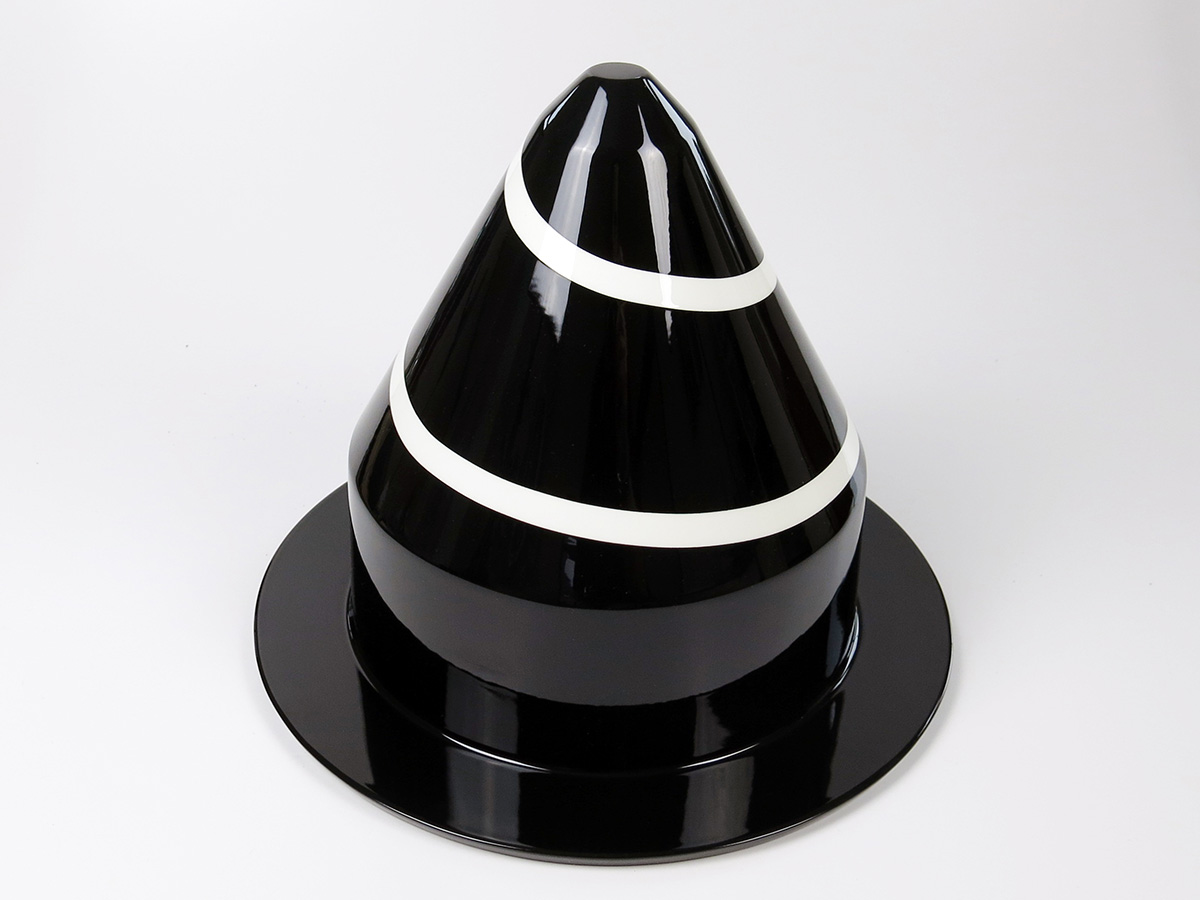
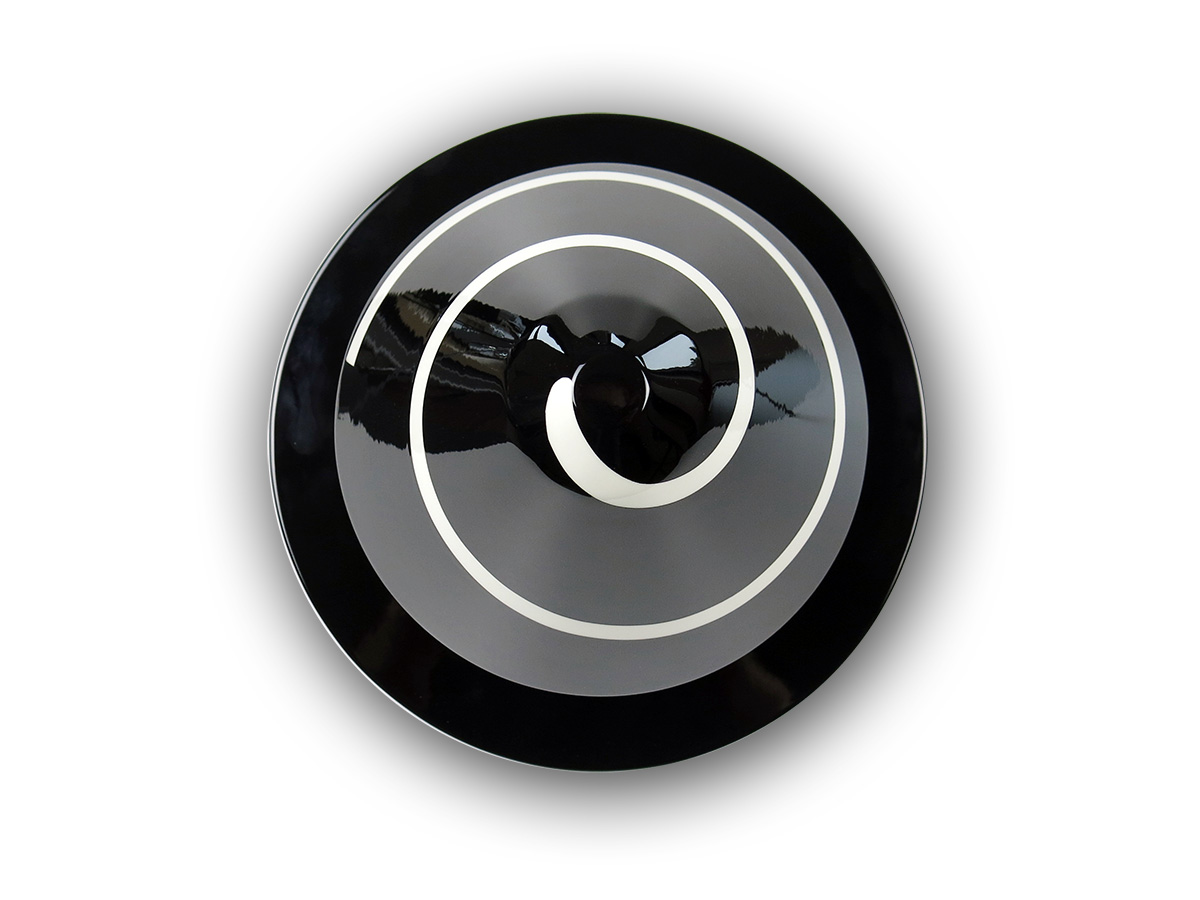
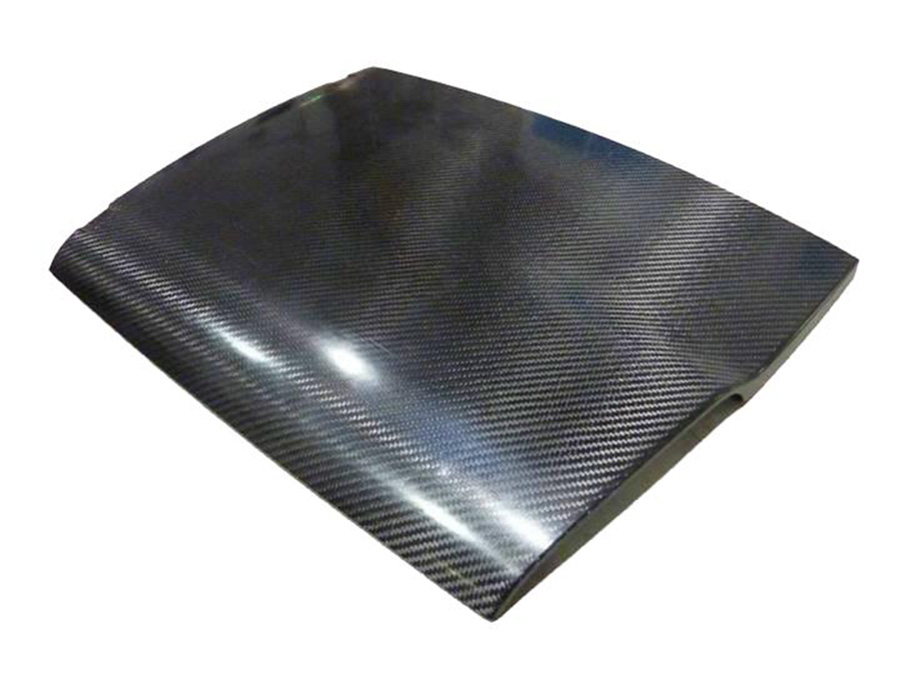
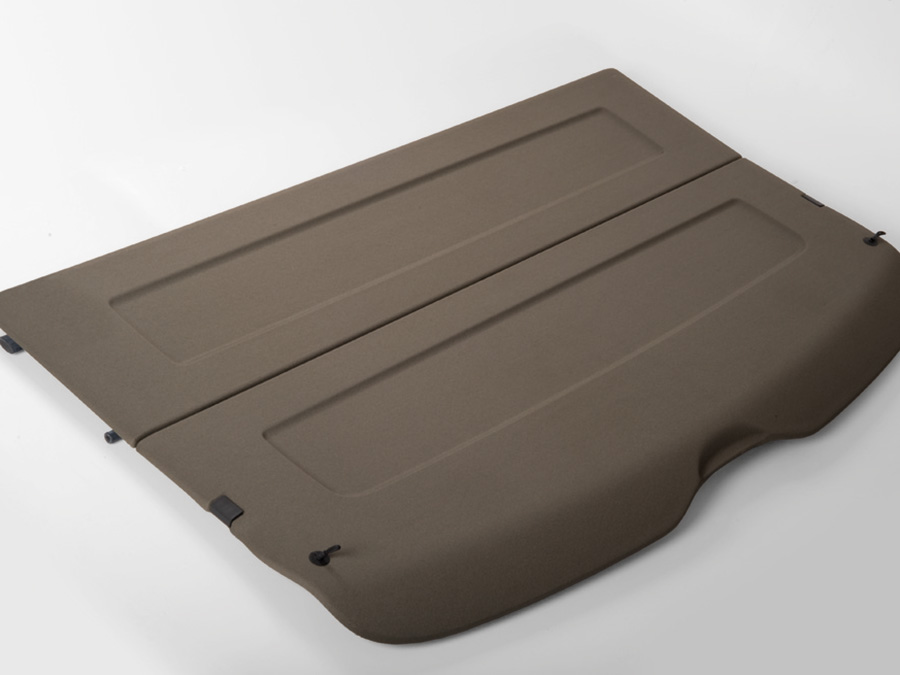
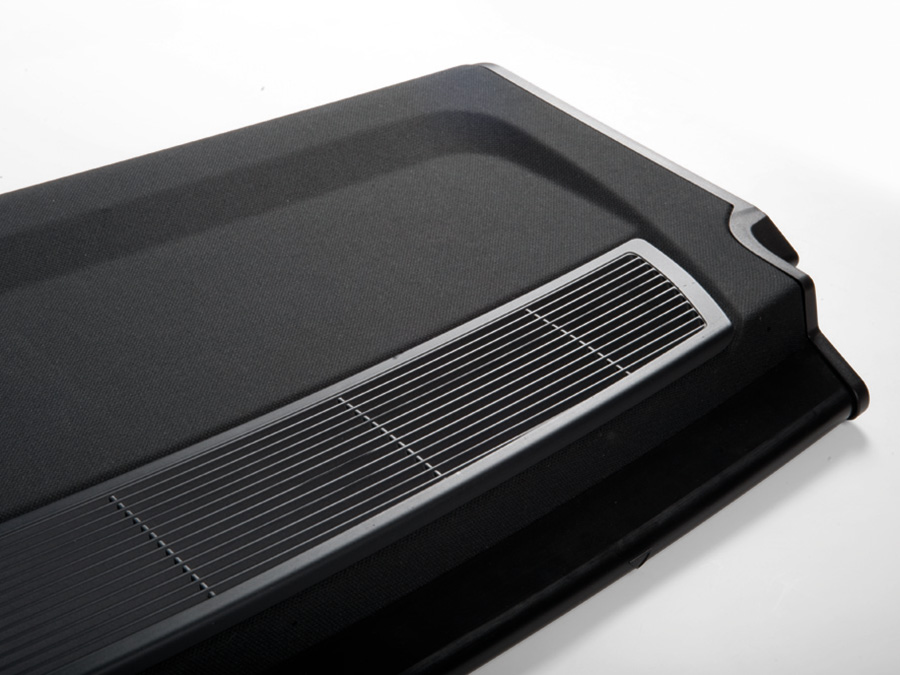
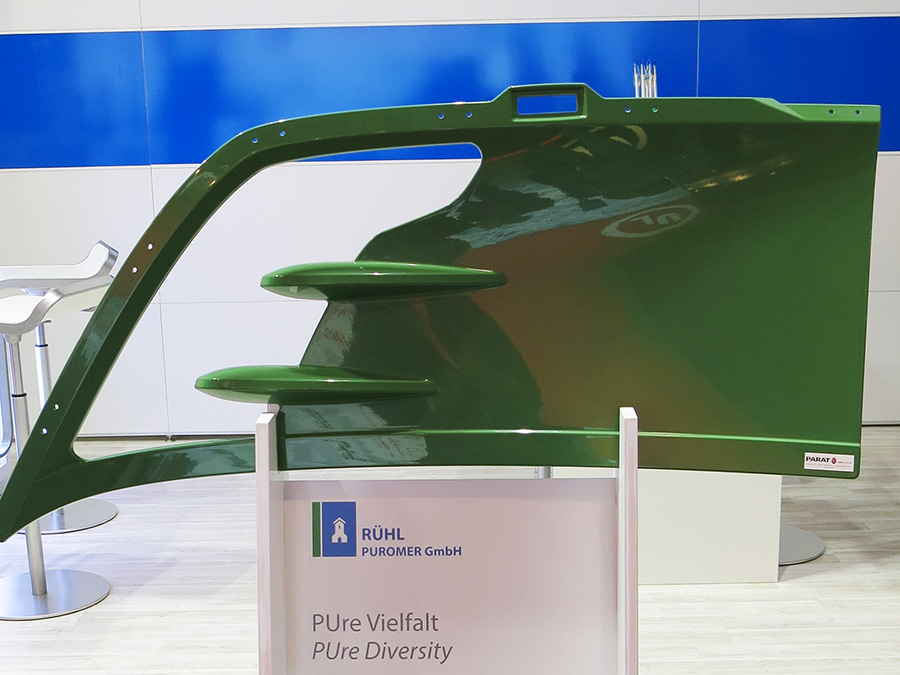
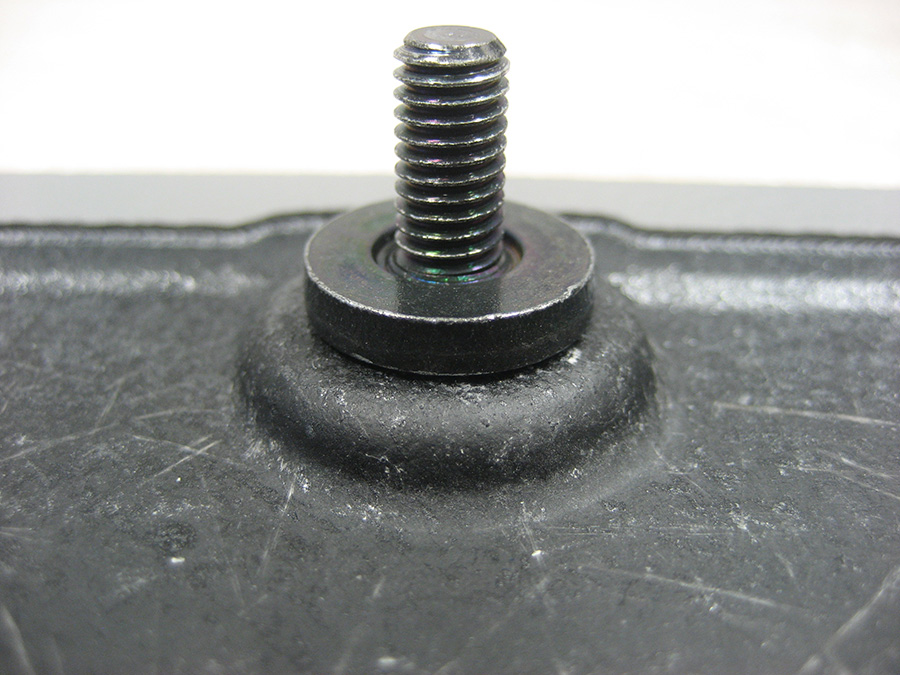
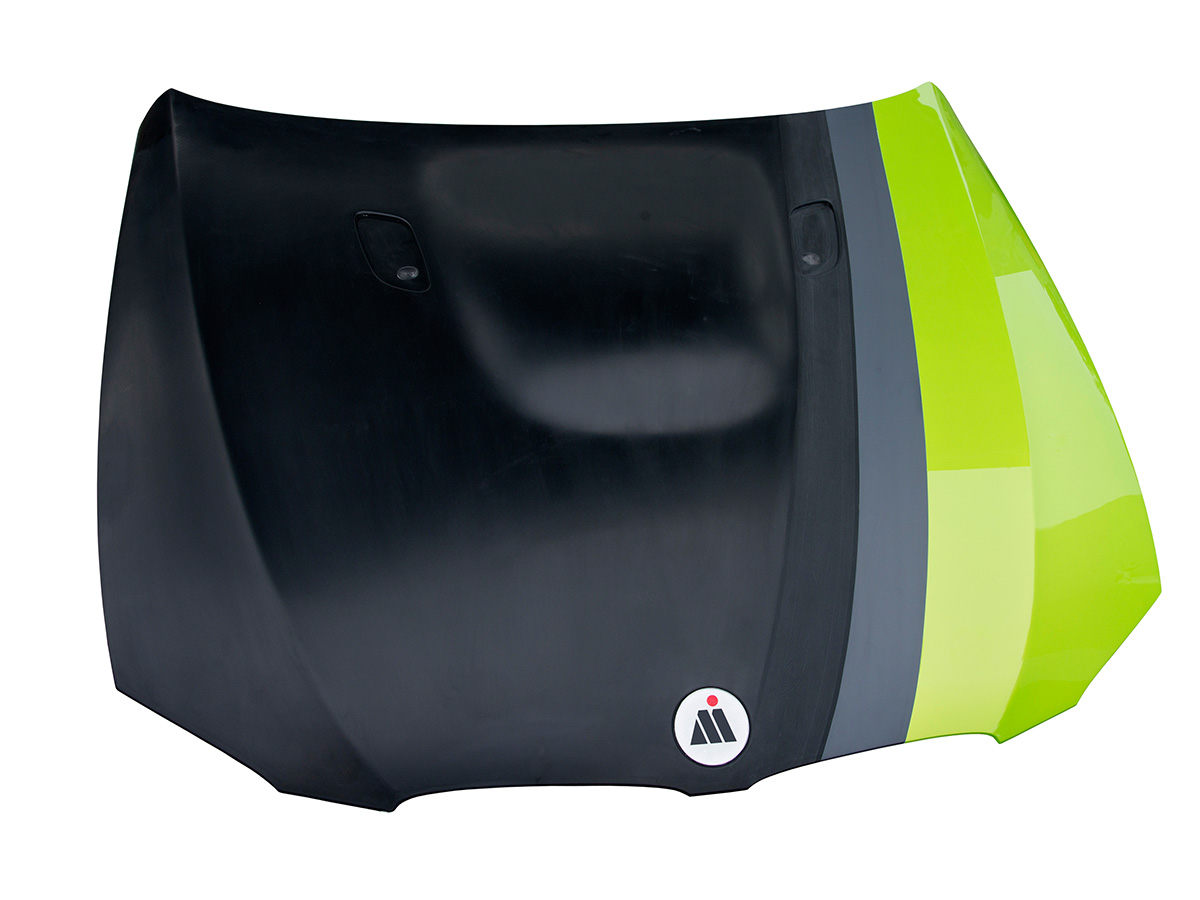
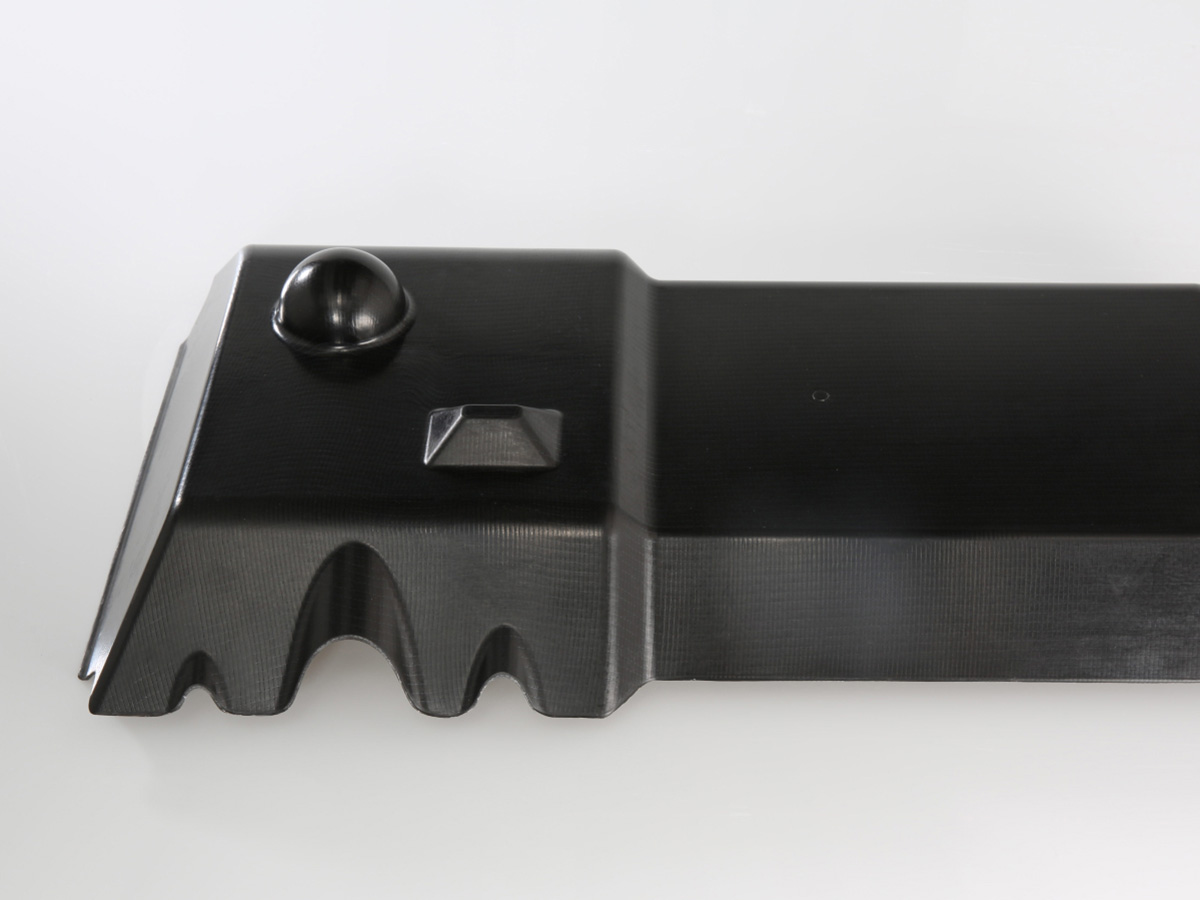
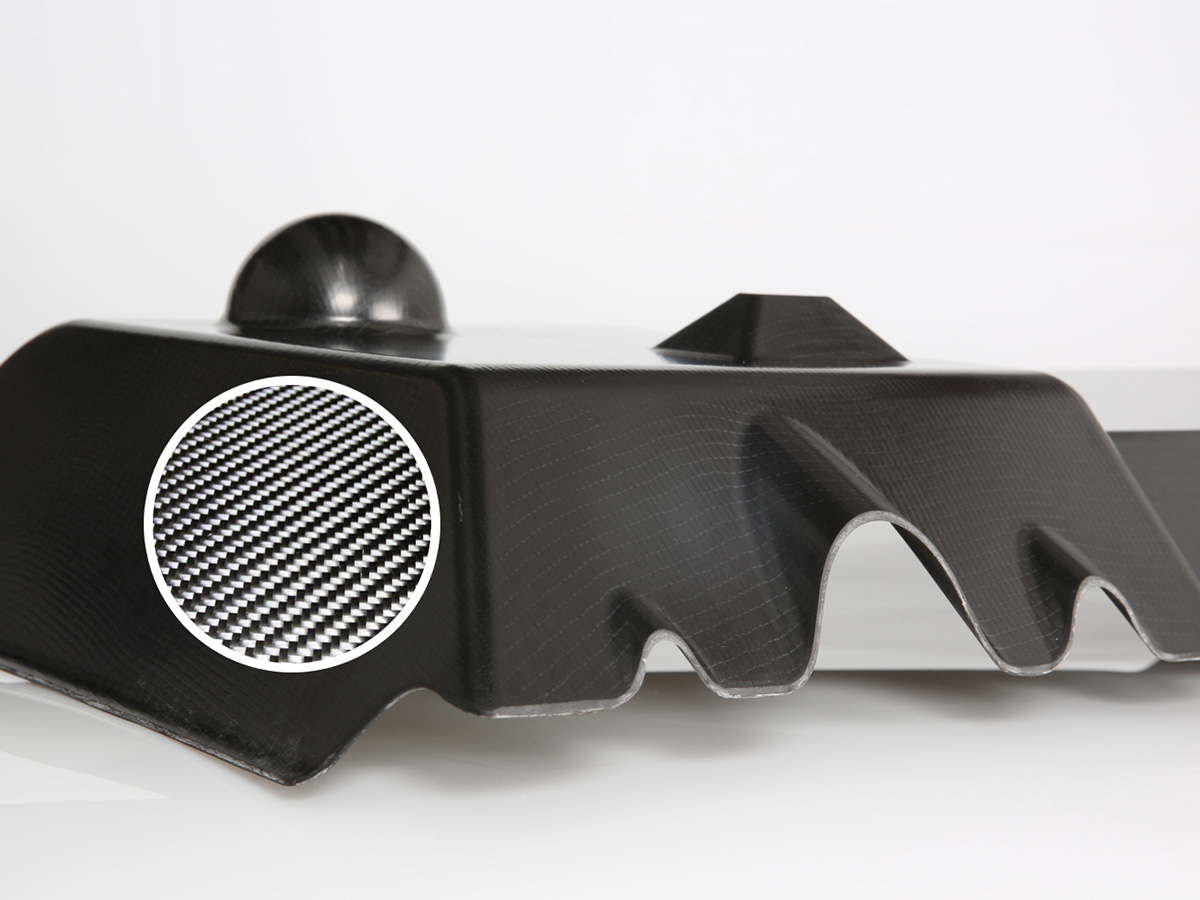
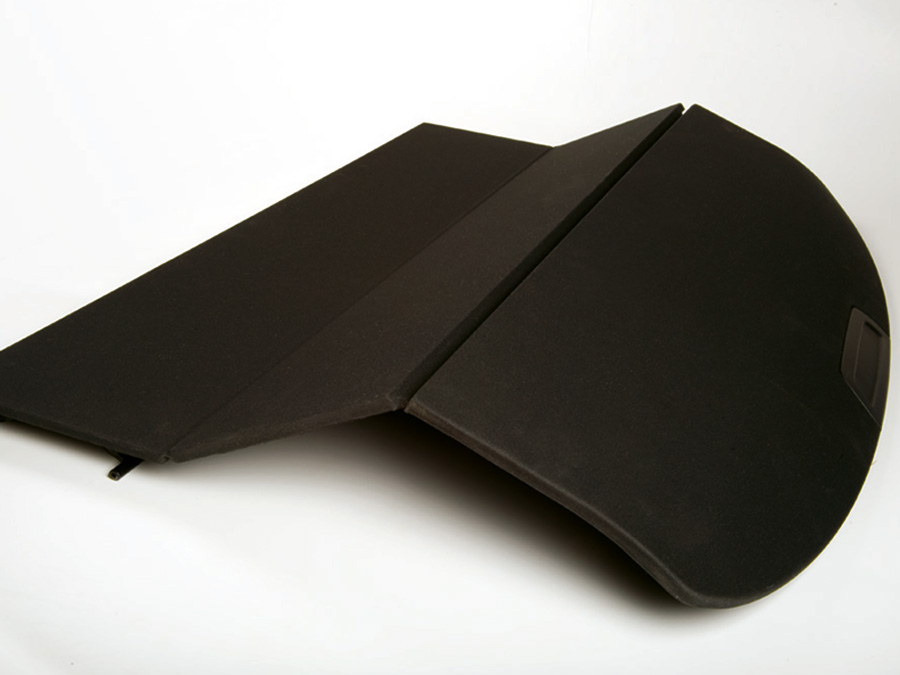